Gears are important mechanical elements used in various sectors, especially industry. With a main function to transfer power and motion between components, there are several types of gears based on functions and characteristics.
Different gear types come with different advantages and are applicable in different equipment. These elements are commonly employed in an extensive range of mechanical devices, such as instrumentation, clocks, equipment, and even motorcycles.
Daftar Isi
What Is a Gear?
Gear is one of machine elements designed with cylindrical or cone shapes. It has teeth with equal spacing around the surface. To make it work, gears can be paired to transmit forces and rotations from the driving equipment to the driven equipment.
Gear has three main functions, including to increase torque from the motor; to reduce the speed produced by the motor; and to change direction of the rotating equipment. Gears can be connected to the gear box using belts, chains, couplings, or hollow shaft.
This element has mechanical characteristics that make it widely used in industry to transmit power of mechanical devices, such as instrumentation, equipment, and clock. With its function to increase or reduce speed, gears are often employed in motorized devices like automobiles and motorcycle.
Gears come in various shapes, such as elliptical, circular, square, and triangular. However, circular is the most common shape widely used in many devices. Circular gears offer constancy in the gear ratios, which means the device provides the same output at the given input.
Meanwhile, devices that use non-circular gears has variable torque and speed ratios. The variable torque and speed aims to fulfill irregular motions, including reversing motion and multi speed. In addition, linear gears are able to convert rotational motion into translational motion.
Various Types of Gears and Applications
There are at least five common types of gears utilized throughout industry, including spur gears; helical gears; bevel gears; worm gears; and rack and pinion. Each gear type comes with different characteristics for different devices and systems.
1. Spur Gears

Spur gears, also known as cylindrical gears, are the most widely used. The gear that belongs to parallel shaft group has cylindrical pitch and straight teeth which are parallel to the shaft. This kind of gear type can reach high accuracy with easy production process.
This gear type is characterized by lack of axial load, high-load handling, high efficiency rates, and high-speed. It can be paired with another spur gear, gear rack, and internal gear depending on the application.
The advantages of using this kind of gear is quite obvious. It provides ease of assembly and efficiency to save a lot of time. Its straight teeth are also easy to align so it does not take extra effort. Additionally, it helps minimize power lost caused by slippage. However, it has high level of stress and noise.
Spur gears are widely used in mechanical applications, such as pumps, clocks, material handling equipment, power plant machinery and watering systems. It is also commonly found in washing machines and dryers. For higher gear reduction, multiple spur gears can be used.
2. Bevel Gears

This is a cone-shaped gear with angled teeth along the surface. These types of gears are employed to transmit power between two intersecting shafts. There are several kinds of bevel gears, such as straight bevel gears, spiral bevel gears, helical bevel gears, miter gears, and more.
Among other types of bevel gears, straight bevel gears are the most used as it has a simple design and easy to manufacture. This teeth of straight bevel gears are designed to engage together at once and gradually. Despite its efficiency, it produces noise and high impact during operation.
Bevel gears are often used in differential drives such as automobile as well as in the main mechanism of a hand drill.
3. Helical Gears

Helical gears are quite similar to spur gears because it uses parallel axes configuration. However, it does not come with straight teeth. Instead, the gears are constructed with winding tooth lines. These angled teeth allow better quietness and higher loads, making it ideal for high speed.
Helical gears that are designed with angled teeth enable them to engage with other gears in a different way than spur gears with straight teeth. The contact level between helical gears increases gradually which allows less impact loading on the teeth. It also produces smoother operation.
There are two main advantages of using helical gears in devices and systems. Aside from giving smooth and quiet operation, this type of gear can be mounted both in parallel and crossed. Not to mention it is capable of handling greater loads. However, helical gears operate with less efficiency.
When it comes to application, helical gears are quite similar to spur gears. Its capability of handling high loads and high speeds make it suitable for devices like generators and pumps. This gear is also ideal for automobile transmissions, thanks to smooth and quiet operation.
4. Worm Gears

Worm gears consist of a worm wheel and a worm that comes in a screw shape cut. This kind of gear is used to deliver power and motion between non-intersecting and non-parallel shafts. Worm gears provide large gear ratios for significant speed reduction.
Cylindrical is the most common shape of worm gears, but some of them come in different designs such as hour-glass. The advantage of worm gears is that it reduces friction for less noise and smoother operation.
This gear type is often found in industry like in heavy equipment and sometimes consumer applications. It is also used in automotive steering system, lifts, and automatic door system.
5. Rack and Pinion Gears

Another type of widely used gear is rack and pinion. This is a pair of gears consisting of a cylindrical gear called pinion and a gear rack that is designed with straight teeth cut. The teeth can be either parallel or angled, depending on the pinion type.
The most obvious advantages of rack and pinion gears are simple design and low cost manufacturing. It also has capabilities to carry high load capacities.
This type of gear is commonly applied in automotive steering system, weighing scales, and transfer systems.There are different types of gears often used in industrial sector. Each gear comes with different characteristics and application for various purposes.
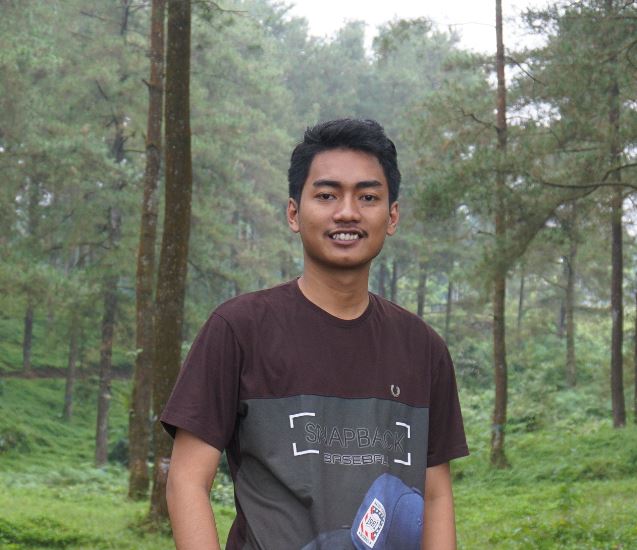
Muhammad Reza Furqoni atau biasa disapa Reza adalah founder dan CEO di teknikece.com Sebelum mendirikan teknikece.com, ia dikenal sebagai seorang mahasiswa dan aktif menulis artikel terkait perkembangan dunia teknologi.